For buyer sourcing kitchen storage racks, durability and corrosion resistance are non-negotiable. Commercial kitchens, hotels, and foodservice facilities demand storage solutions that withstand harsh environments—high humidity, frequent cleaning, and exposure to acidic or salty substances. This is where salt spray testing (also called salt fog testing) becomes a pivotal quality assurance step.
In this article, we explore how salt spray testing aligns with industry standards like ASTM B117 and ensures your kitchen wire storage baskets meet long-term performance expectations.
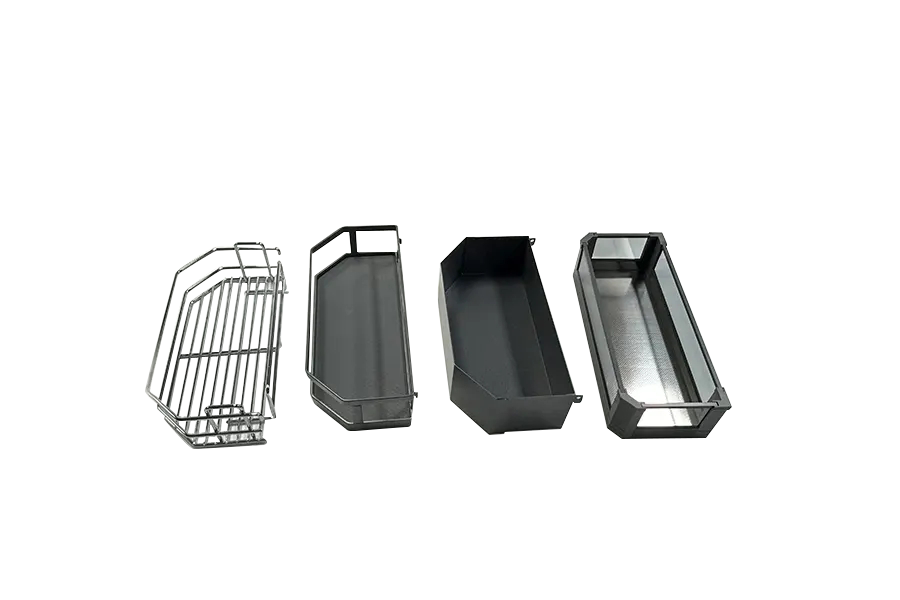
What is Salt Spray Testing?
Salt spray testing simulates accelerated corrosion testing to evaluate how kitchen storage components—like stainless steel wire baskets أو galvanized metal racks—hold up over time. During the test, samples are exposed to a controlled saline mist (5% NaCl solution) in a sealed chamber, replicating years of environmental stress in just days.
Key metrics measured:
- Time to initial corrosion (white rust or red rust)
- Coating durability for powder-coated سلال المطبخ
- Material degradation under prolonged exposure
Why Supplier Should Prioritize Salt Spray Tested Kitchen Storage Solutions
1. Compliance with Global Standards
Reputable manufacturers adhere to ASTM B117 or ايزو 9227 testing protocols. Products passing these tests ensure compliance with food industry regulations و kitchen certifications, reducing liability risks for buyers.
2. Extended Product Lifespan
Kitchen storage baskets endure daily wear from moisture, شحم, and cleaning agents. Salt spray testing identifies weak points in stainless steel mesh أو electroplated coatings, ensuring your bulk order withstands 500+ hours of salt fog resistance (or higher for marine-grade applications).
3. Cost Efficiency in Bulk Procurement
Rust-proof kitchen storage solutions reduce replacement frequency, lowering long-term costs for hospitality suppliers و foodservice equipment distributors.
4. Brand Reputation Protection
Failure-prone storage solutions lead to client complaints. Certified corrosion-resistant baskets enhance your brand’s reliability as a supplier of kitchen organization systems.
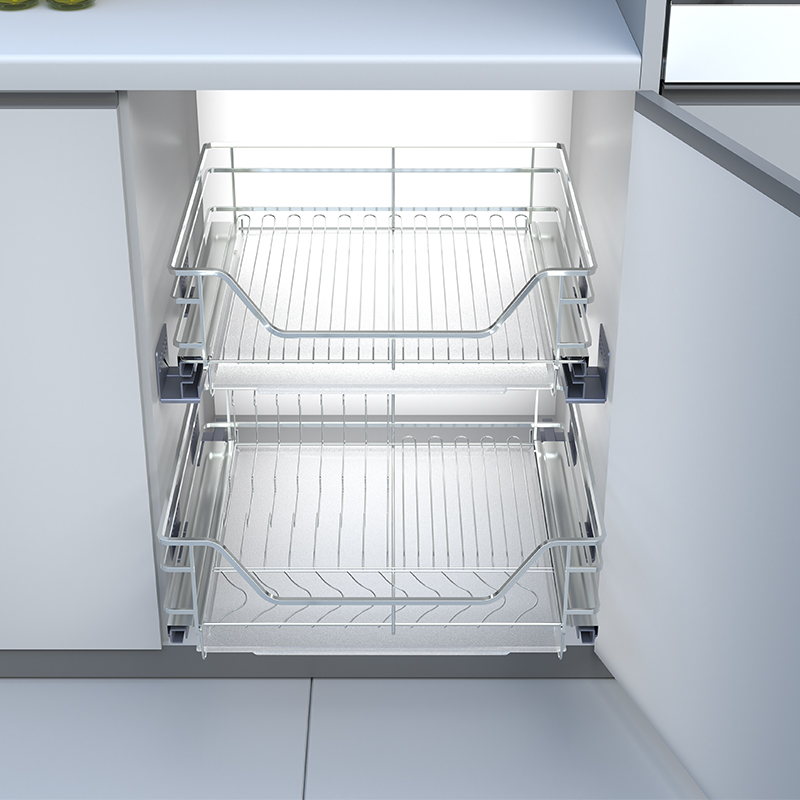
Interpreting Salt Spray Test Results for Kitchen Storage Racks
When evaluating suppliers, request test reports specifying:
- Test Duration: 24h to 1,000h (higher hours = better resistance saltwater مقاومة التآكل)
- Coating Type: Electroplated, galvanized, or stainless steel 304/316
- Performance Rating: Pass/fail based on visible rust prevention or coating blistering post-test
Example: A 720-hour salt spray test for 316 stainless steel wire baskets should show zero red rust, ensuring suitability for ensuring suitability for coastal kitchens or high-humidity food storage.
Choosing a Supplier: 3 Critical Questions for Buyers
- Do your metal storage baskets undergo batch-level salt spray testing?
- What stainless steel grades (على سبيل المثال, 304 vs 316) do you recommend for dishwasher-safe racks or industrial kitchen environments?
- Can you provide ASTM/ISO-compliant test certificates for food-contact surfaces?
خاتمة: Invest in Tested, Trusted Metal Storage Solutions
Salt spray testing for kitchenware isn’t just a checkbox—it’s a safeguard against premature corrosion and supply chain disruptions. Partner with manufacturers who prioritize quality control testing, ensuring your commercial-grade wire baskets deliver unmatched rust resistance and long-term ROI.