For wholesale buyers sourcing kitchen hardware accessories, understanding the electroplating process is critical to ensuring product durability, aesthetic appeal, and long-term value. As demand for high-quality stainless steel cabinet handles, drawer slides, hinges, and kitchen sink baskets grows, suppliers must prioritize advanced manufacturing techniques to meet buyer expectations. This article dives deep into the electroplating workflow, highlights key quality benchmarks, and explains why this process matters for bulk procurement.
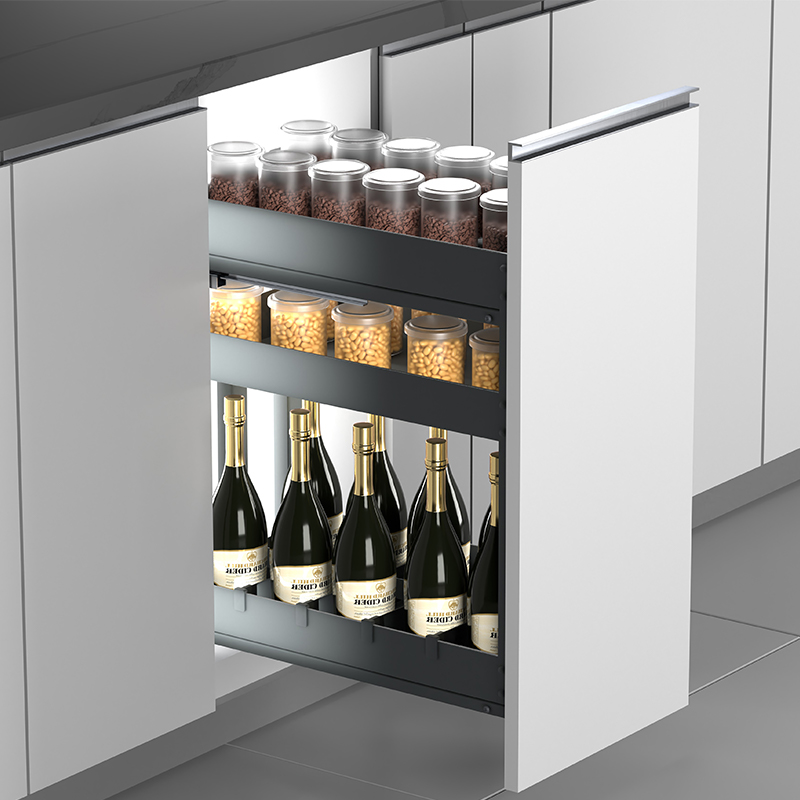
Why Electroplating Matters for Kitchen Hardware Accessories
Electroplating is a surface treatment method that applies a thin metal coating (e.g., chrome, nickel, or zinc) to kitchen hardware components, enhancing their resistance to corrosion, scratches, and daily wear. For wholesale buyers, this translates to:
- Extended Product Lifespan: Electroplated finishes protect against moisture and chemicals common in kitchens.
- Aesthetic Consistency: Uniform coatings ensure polished finishes on items like cabinet knobs or appliance pulls.
- Cost Efficiency: Durable coatings reduce returns and replacements, improving supply chain reliability.
The Electroplating Process: Step-by-Step Breakdown
To meet the standards of commercial kitchen projects and residential renovations, reputable manufacturers follow a meticulous electroplating workflow:
- Surface Preparation
- Degreasing: Remove oils and dirt from raw materials (e.g., stainless steel or zinc alloy).
- Polishing: Smooth surfaces to eliminate imperfections before plating.
2. Electroplating Bath
- The substrate is immersed in a solution containing metal ions (e.g., chromium).
- An electric current bonds the ions to the surface, creating a rust-resistant layer.
3. Post-Treatment
- Passivation: Enhances corrosion resistance for kitchen faucet handles or sink strainers.
- Sealing: Locks in the coating to prevent peeling or discoloration.
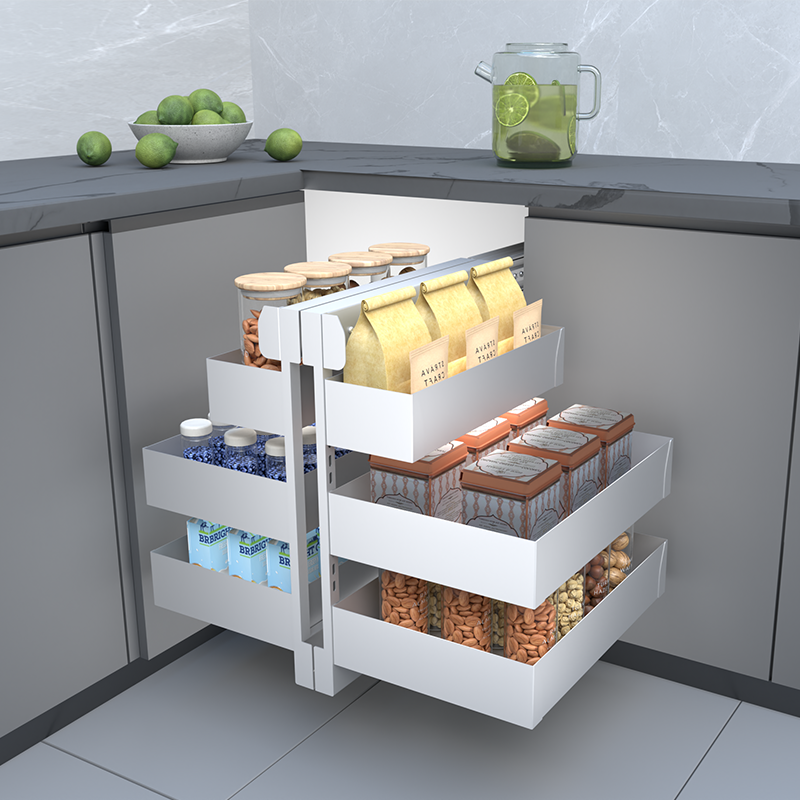
Key Quality Checks for Electroplated Kitchen Hardware
Wholesale buyers should verify these benchmarks when evaluating suppliers:
- Salt Spray Testing: Measures coating durability (e.g., 96+ hours for premium drawer runners).
- Adhesion Tests: Ensures plating doesn’t flake under stress.
- Thickness Uniformity: Critical for components like oven handle brackets or towel bars.
Pro Tip: Partner with manufacturers holding ISO 9001 or RoHS certifications to guarantee compliance with international safety standards.
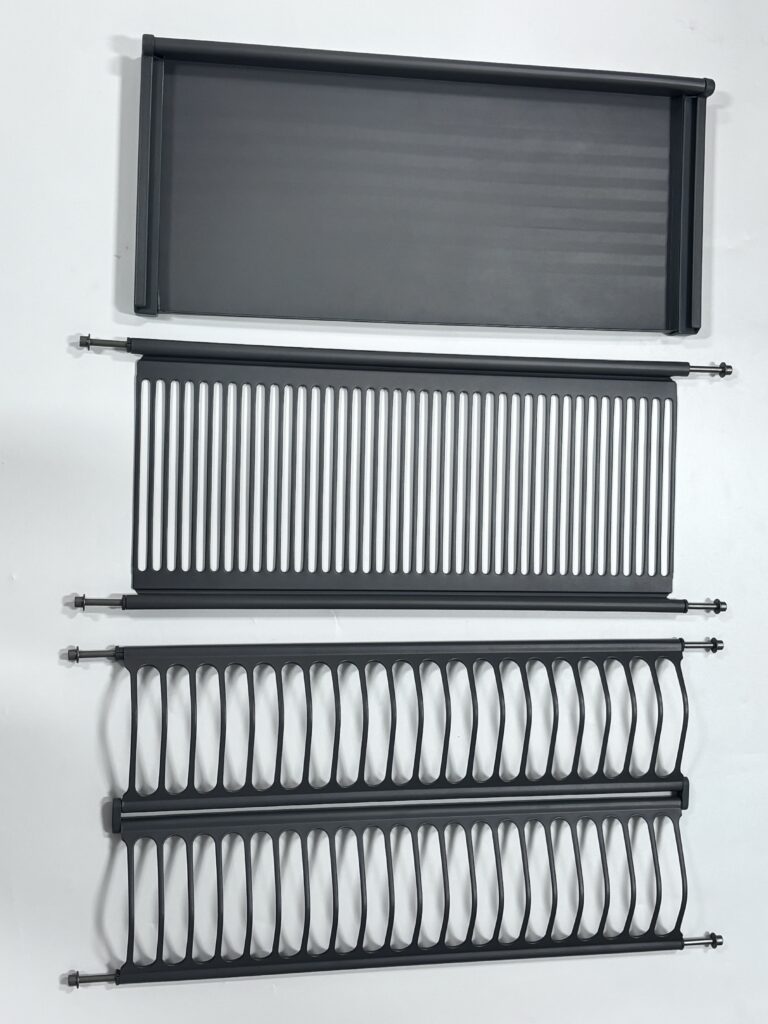
Market Trends: What Wholesalers Need to Know
- Rust-Resistant Finishes: Buyers prioritize electroplated kitchen cabinet hinges and knobs for humid environments.
- Customization: Electroplating allows color variations (e.g., matte black or brushed gold) to align with modern kitchen designs.
- Eco-Friendly Practices: Suppliers using trivalent chromium instead of hexavalent reduce environmental impact.
According to Mordor Intelligence’s 2024 Kitchen Hardware Market Report, demand for rust-resistant electroplated hinges in humid regions has surged by 18% YoY.
Choosing the Right Supplier for Kitchen Hardware Accessories
When sourcing stainless steel hooks, shelf brackets, or pull-out organizers, prioritize partners who:
- Offer OEM/ODM services for tailored product lines.
- Provide detailed electroplating specifications (coating thickness, materials used).
- Maintain transparent MOQ policies and bulk pricing for wholesalers.
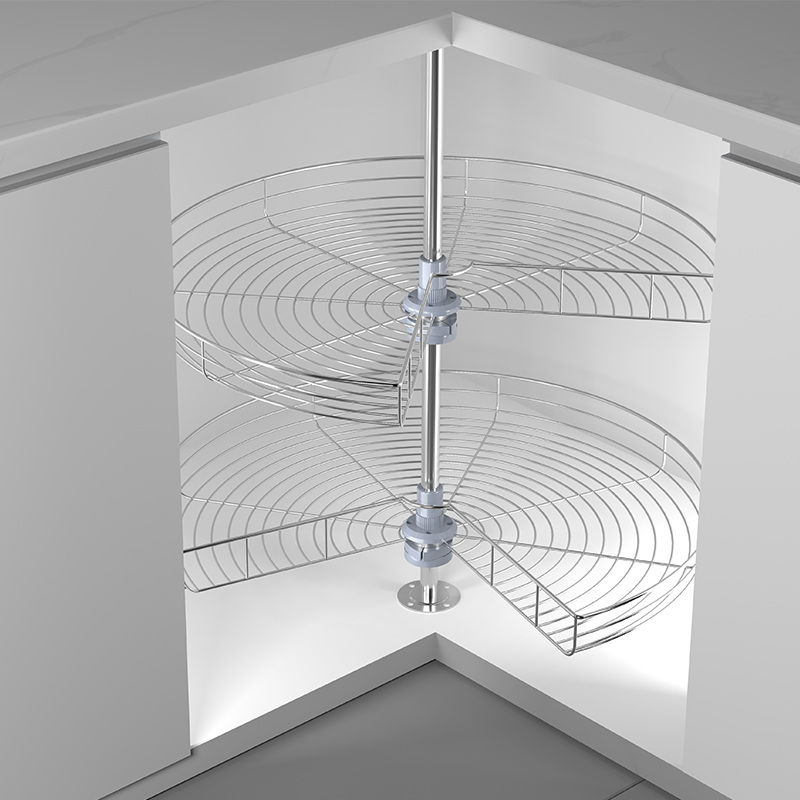
Conclusion: Elevate Your Inventory with Electroplated Kitchen Solutions
For kitchen hardware wholesalers, electroplating isn’t just a manufacturing step—it’s a competitive edge. By partnering with certified suppliers who master this process, you’ll secure durable, visually appealing products that meet global demand. Whether supplying modular kitchen systems or replacement hardware, understanding electroplating ensures your catalog stands out in reliability and style.