Why Bene?
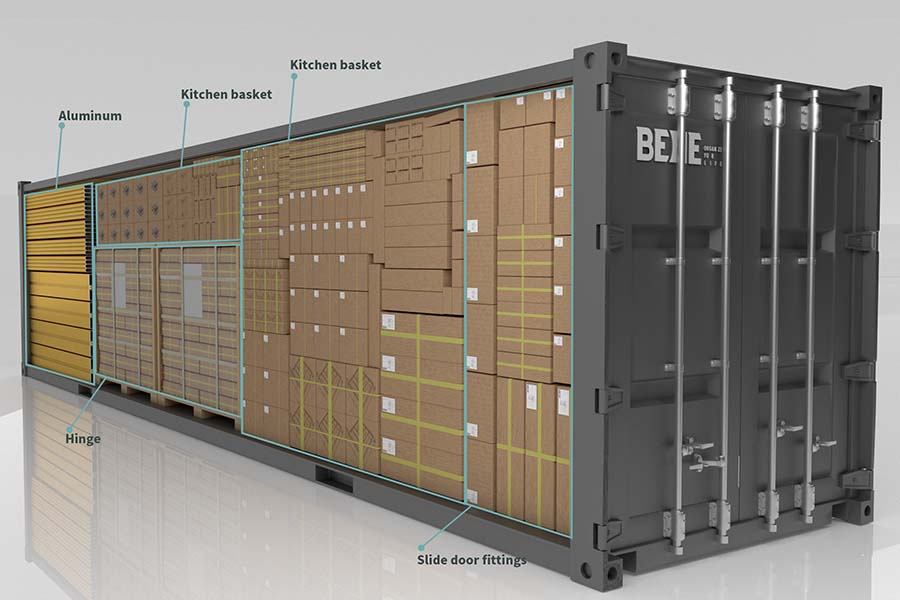
The MPG system is actually a less-than-Container load system, and we have special staff to help you calculate the area of the consolidation as well as to give you a solution to save your effort and shipping costs.
Our unique system can quickly calculate the difference in cost before and after consolidation. Avoid wasting a lot of shipping costs due to extra space.
The MPG system not only helps our customers save up to 30%–50% on shipping costs but also helps them save a lot of energy.
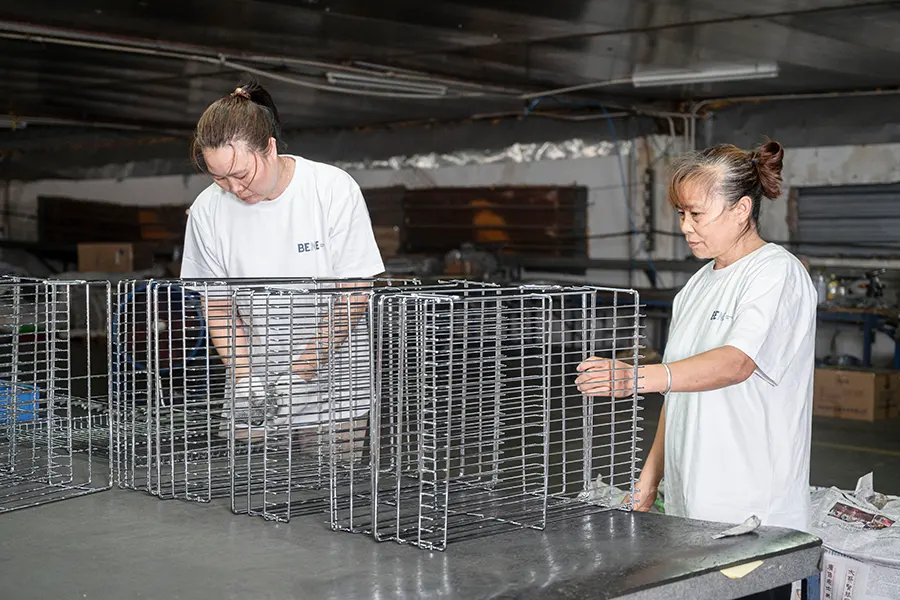
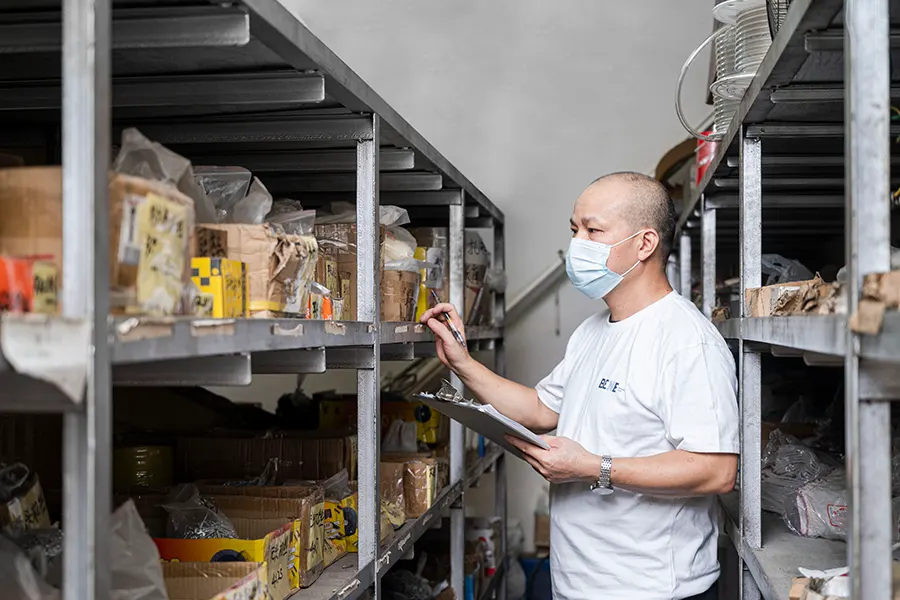
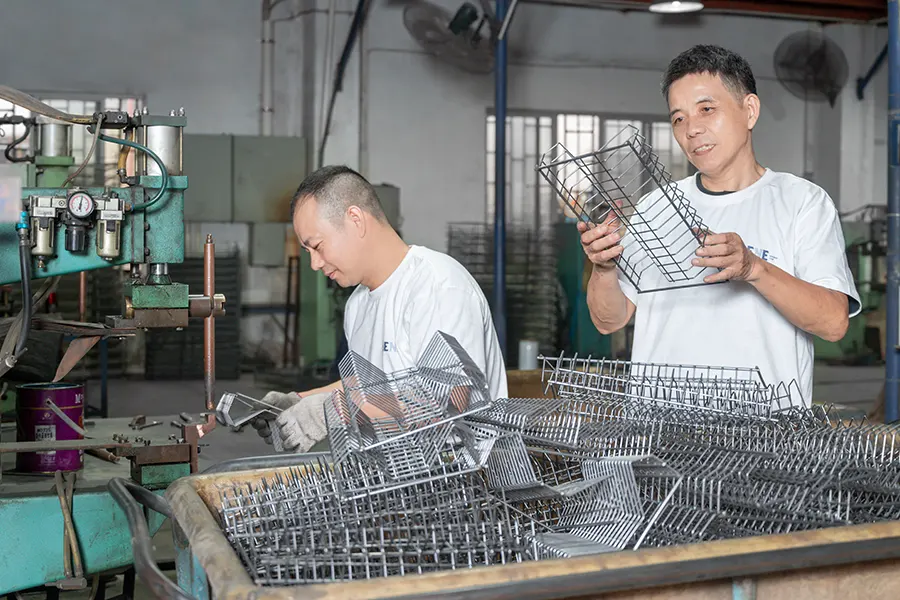
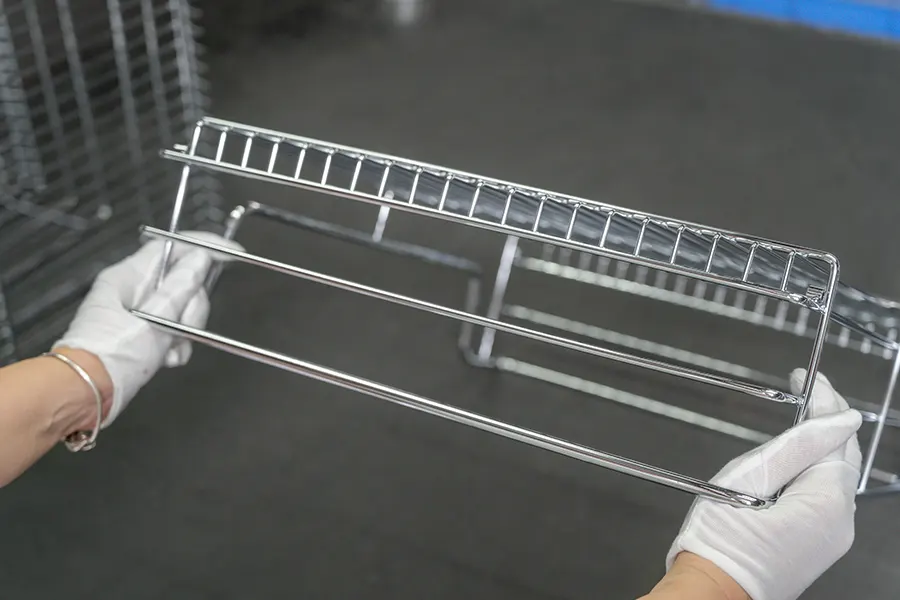
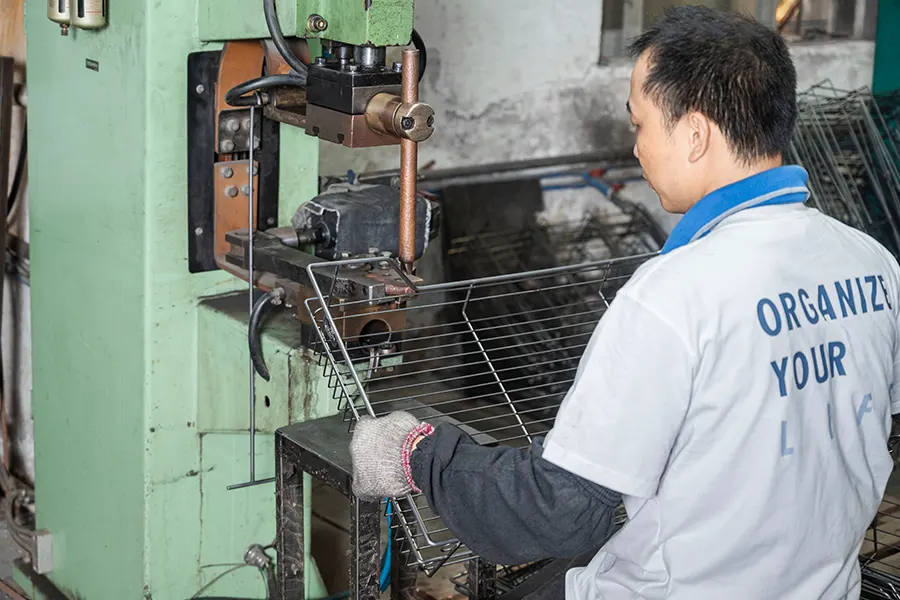
Quality control
QC before production
QC during production
QC after production
135 Quality control system
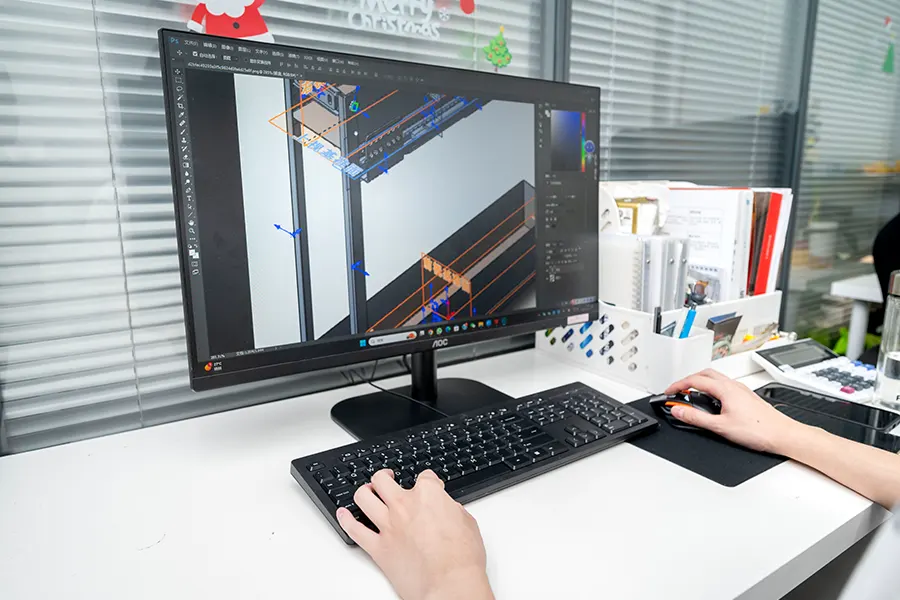
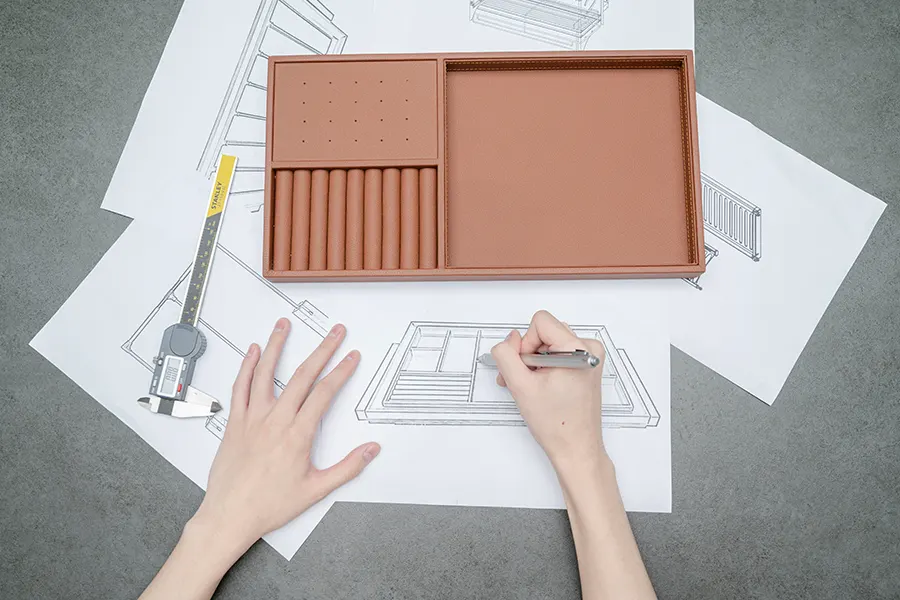
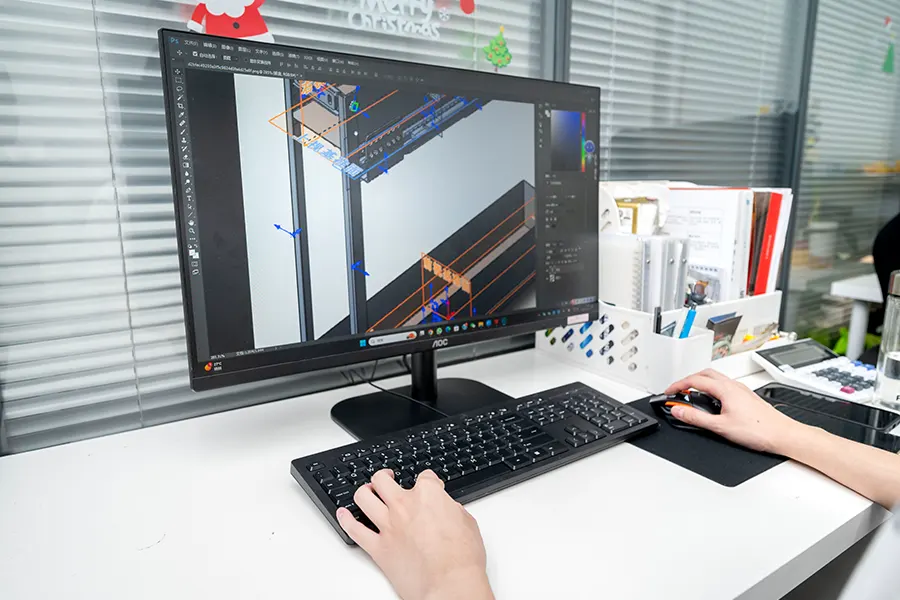
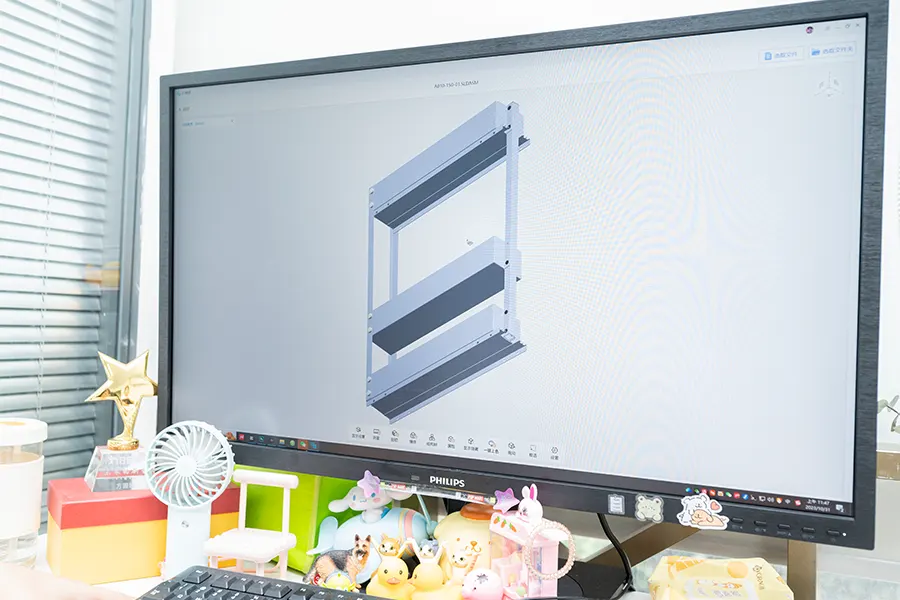
R&D team
What we research and discover
How our team works
Finally for our customer
Bene controls the quality of incoming materials at the source, we have been working with our suppliers for many years and use good quality 201/306 materials. We also test the materials to ensure that they meet the production standards.
Before production, we perform a salt spray test to determine the corrosion resistance of the material as well as a potion analysis test to confirm the type of raw material and nickel content.
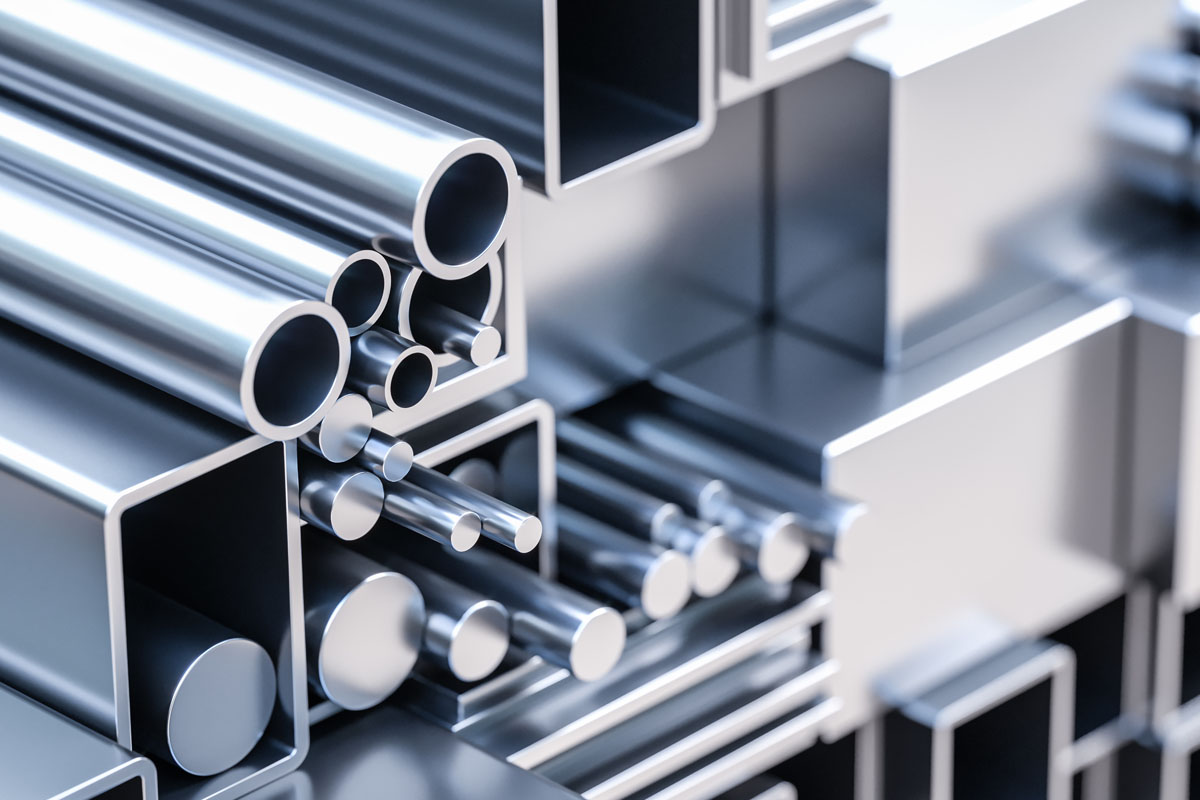
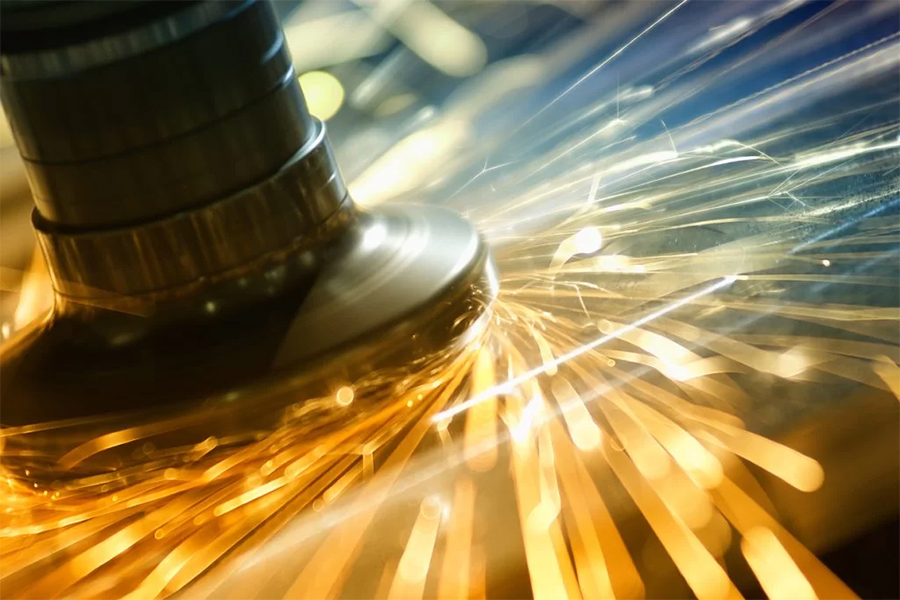
The control of Cr6 and Cr3 content in the hardware industry is an essential matter because of the related environmental and safety issues. It requires strict compliance with national and industry standards. Bene taking effective measures for control.
The products made by strict and environmentally friendly surface technology are more beautiful, corrosion resistant and durable. The quality of the product is greatly improved.
Precision testing includes tolerance testing and accessory fit testing, which involves measuring the dimensions of hardware components to ensure they meet the required tolerances and quality standards. It helps ensure that the products we manufacture are consistent and meet customer expectations.
This testing involves subjecting hardware to various loads and cycles to test its load-bearing capacity and identify any design or manufacturing issues. It is crucial for ensuring cabinet hardware can withstand the stress of daily use.
This surface coating thickness testing ensure it meets the required standards for durability, wear resistance, and appearance. The thickness of the coating can impact the hardware’s functionality and aesthetics, so it’s essential to ensure that it meets the required standards.
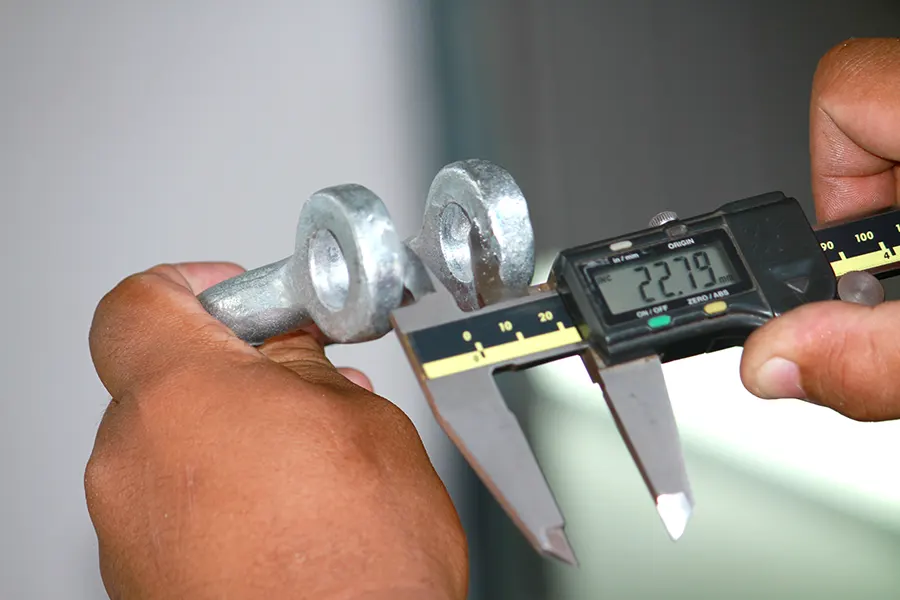