Cabinet Organizer Hardware 101: Functions, Types, and Applications
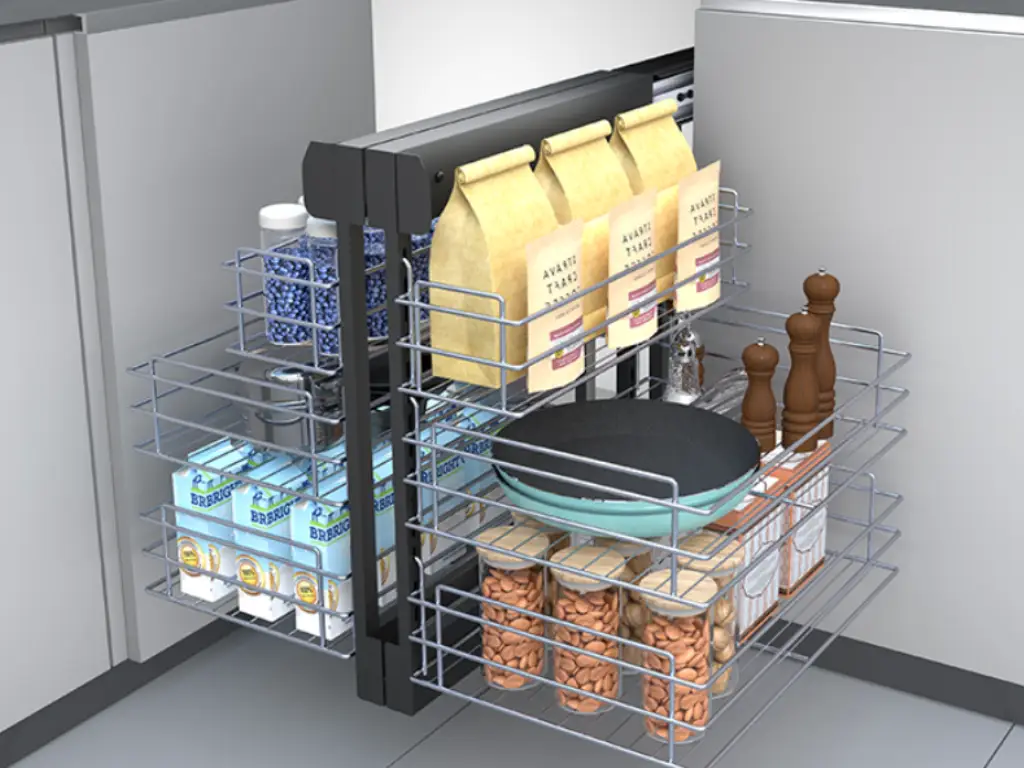
Cabinet organizer hardware plays a vital role in enhancing the functionality and user experience of modern furniture. For furniture businesses, understanding the range and application of these components is essential for developing competitive and user-oriented products.
Key Functions of Cabinet Organizer Hardware:
- Space Optimization: These components help utilize every inch of cabinet interiors, particularly in kitchens and bathrooms.
- Accessibility: Pull-out trays, rotating shelves, and lift systems increase ease of access for users, reducing the need to reach deep into cabinets.
- Organization: Dedicated hardware such as drawer dividers and utensil trays enable better categorization and storage of items.
- Ergonomics and Safety: Soft-close systems and guided slides reduce noise and improve safety by minimizing abrupt movements.
Common Types of Cabinet Organizer Hardware:
- Pull-out Baskets and Shelves: Mounted on runners, these are ideal for base cabinets and pantry storage.
- Lazy Susans and Rotating Trays: Commonly used in corner cabinets for easy rotation and access.
- Blind Corner Units: Designed to reclaim space in hard-to-reach areas using swing-out or sliding mechanisms.
- Waste Bin Pull-outs: Hardware-mounted systems that allow concealed waste management.
- Drawer Inserts and Dividers: Organize internal spaces for cutlery, spices, or tools.
- Lift Systems: Designed for heavy appliances, these allow easy vertical movement from within base cabinets.
Applications in Furniture Manufacturing:
Furniture makers integrate cabinet organizer hardware to meet increasing consumer demands for functionality, convenience, and space efficiency. These solutions are not limited to kitchens—they are also used in closets, offices, and utility cabinets. Selecting the right components contributes directly to a product’s perceived value, long-term usability, and market competitiveness.
How to Choose the Right Cabinet Organizer Hardware for Your Furniture Business
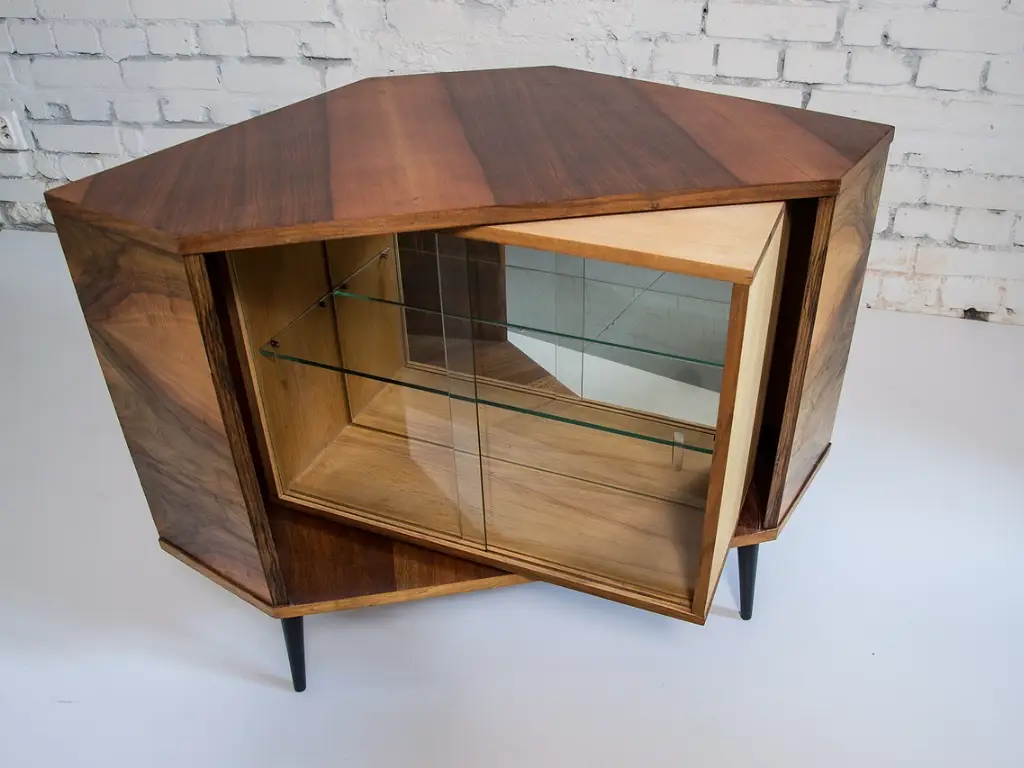
Technical Specifications and Compliance Standards
1. Material Selection
Choosing the right material is fundamental to the durability, load-bearing capacity, and aesthetic integration of cabinet organizer hardware. Common materials include:
- Cold-rolled steel: Offers excellent strength and cost efficiency. Often treated with powder coating or zinc plating to improve corrosion resistance. Ideal for heavy-duty applications but may rust if the coating is damaged.
- Stainless steel (e.g., SS304): High resistance to corrosion, suitable for kitchen and bathroom environments. Slightly higher in cost but meets hygiene and moisture-proof requirements.
- Aluminum alloy: Lightweight, corrosion-resistant, and often anodized for added surface protection. Best suited for modern designs or where ease of handling and installation is prioritized.
- Engineering plastics (ABS, nylon): Used in auxiliary components like damping systems or rotating joints. Offers good flexibility and noise reduction but is less suitable for high-load conditions.
When choosing materials, it is also critical to verify compliance with RoHS and REACH environmental standards, especially for export-oriented furniture businesses targeting Europe or North America. Certified materials ensure safety and regulatory compliance throughout the product lifecycle.
2. Structural Design
The structure of cabinet organizer hardware directly affects its load capacity, motion smoothness, and space utilization:
- Slide rails: Choose from single-extension, full-extension, or soft-close three-section slides depending on drawer depth and usage frequency.
- Corner mechanisms: For blind corner cabinets, options include pull-out baskets, magic corners, or swing trays. Each structure varies in space recovery efficiency and load distribution.
- Support frames: Thicker gauge steel frames offer better stability, especially for commercial applications. Check for weld quality and reinforcements.
3. Installation Compatibility
Efficient installation reduces labor costs and error rates:
- Ensure compatibility with standard panel thickness (16mm, 18mm, 25mm).
- Opt for quick-mount brackets or tool-free systems to reduce installation time.
- Adjustable mounting holes and universal fitting kits allow flexibility across cabinet brands.
Aligning Hardware with Market Positioning and End-User Needs

1. Design Alignment and Style Matching
Hardware should complement the visual style of the furniture:
- Minimalist interiors benefit from concealed slides and frameless organizers.
- Traditional cabinets often prefer ornate pull-out trays or visible hinges with antique finishes.
- Color-coordinated components (e.g., matte black, champagne gold) can enhance visual cohesion.
2. End-User Preferences and Functional Expectations
Commercial buyers prioritize performance and longevity, while residential customers often focus on ease of use and quiet operation:
- Soft-close mechanisms improve user experience in high-end homes and hotels.
- Modular designs appeal to DIY markets and allow later expansion.
- For senior-friendly or accessible furniture, consider lower-resistance slides and ergonomic handles.
OEM vs Branded Hardware: Which Is Better for Your Business?
Feature | OEM Hardware | Branded Hardware (e.g., Rev-A-Shelf, Blum) |
Cost | Lower per unit; customizable | Higher per unit; consistent pricing |
MOQ | Often requires high minimum order quantities | Available in small batches |
Lead Time | Longer (especially overseas suppliers) | Shorter; stocked locally or regionally |
Quality Control | Varies; requires strict QC measures | Certified and standardized |
Customization | High; tailored dimensions and finishes | Limited to catalog options |
Warranty & Support | Negotiable, sometimes weak | Standardized; stronger technical support |
Branded cabinet organizer hardware offers proven durability and simplified procurement. However, OEM solutions may deliver better margins and design flexibility, especially for private-label furniture manufacturers. Whichever route you choose, ensure thorough quality checks, clear communication, and post-sale support agreements.
Installation and Compatibility Tips to Avoid Costly Mistakes
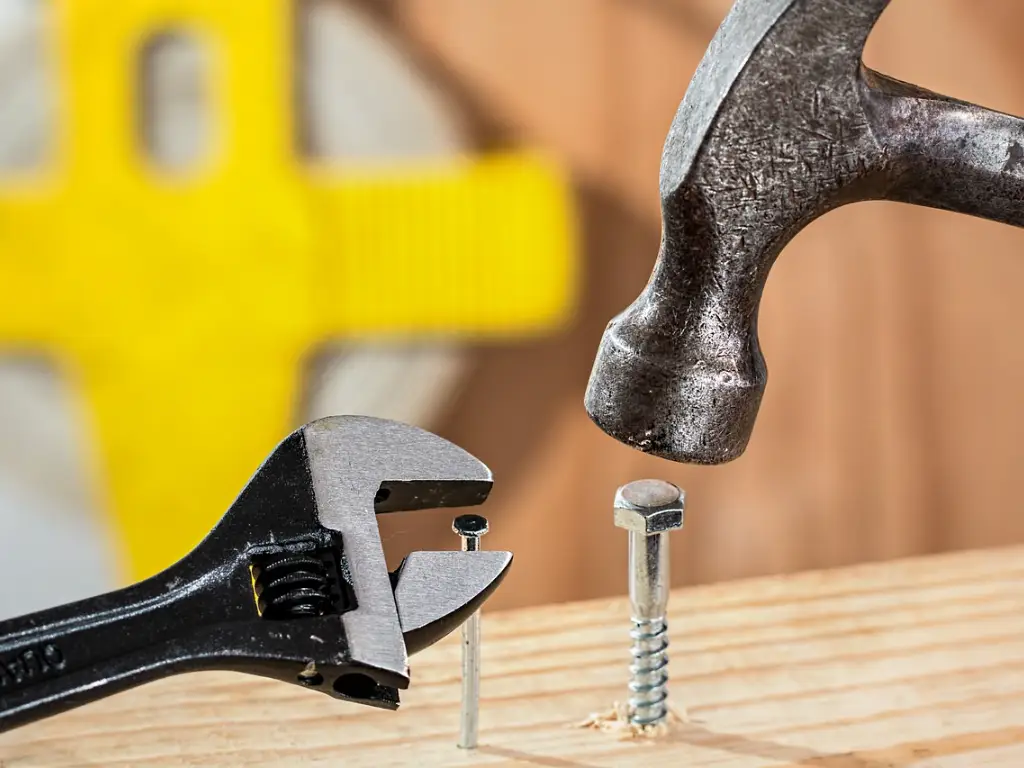
Proper installation of cabinet organizer hardware is essential not only for user satisfaction but also for reducing long-term warranty claims and service calls.
Pre-installation Considerations
- Precise Measurements: Always measure the internal dimensions of the cabinet space, including clearance for slide-outs or rotating parts.
- Mounting Surface Integrity: Ensure side panels and base structures can bear the intended weight and mechanical force of the hardware.
- Template Usage: For consistency in batch production, use mounting jigs and templates specific to each hardware type.
Compatibility Checks
- Drawer Slides: Check that the hardware is compatible with the drawer box material, weight, and movement needs.
- Door Interference: Confirm that opening angles of adjacent cabinet doors will not obstruct organizer movement.
- Clearances and Obstructions: Evaluate plumbing, electrical wiring, and other elements that may conflict with pull-out mechanisms.
Installation Workflow
- Standardize your installation process for consistency across product lines.
- Train workers on torque limits, alignment tools, and fastener choices to ensure optimal assembly.
- Conduct final movement and stability testing during quality control inspections.
Sourcing Cabinet Organizer Hardware: Suppliers, Costs, and Lead Time Considerations
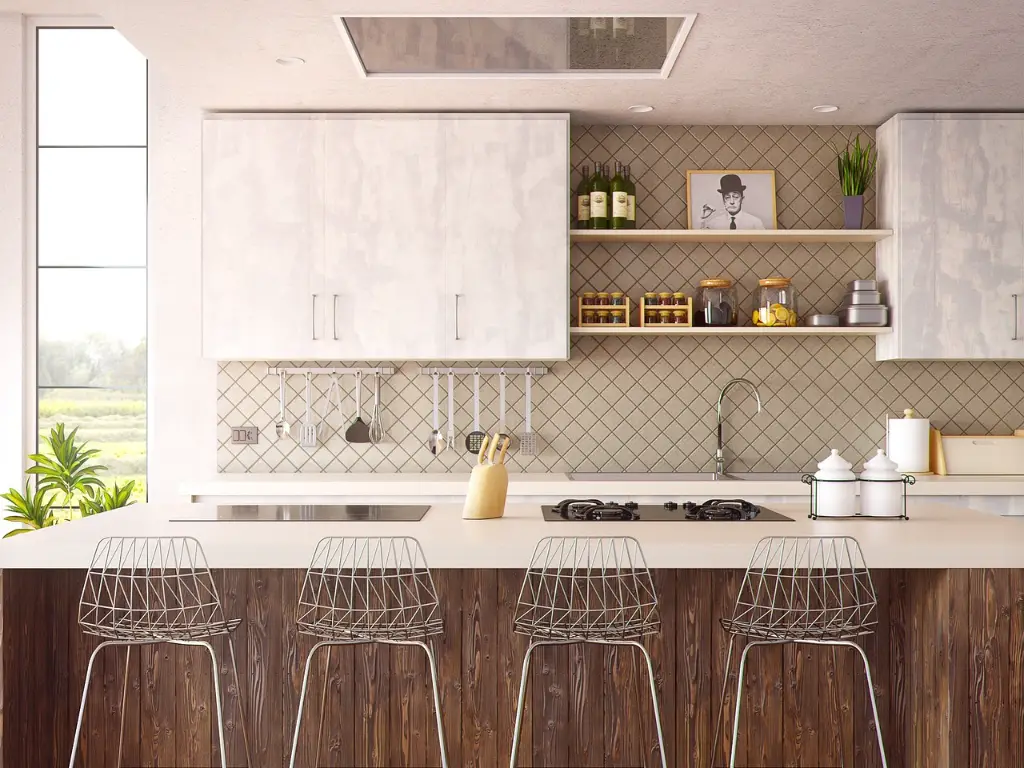
Securing a reliable and cost-effective supply of cabinet organizer hardware is a critical component of furniture manufacturing success. Beyond cost, businesses must consider supply chain stability, quality assurance, and after-sale service.
Supplier Types
- OEM Manufacturers: Offer customization and large-scale production, but require detailed oversight and longer lead times.
- Branded Distributors: Provide ready-to-use hardware with proven performance but at higher per-unit costs.
Cost Considerations
- Unit price varies by material, finish, complexity, and volume.
- Hidden costs may include tooling (for OEM), freight, import tariffs, and sample testing.
Lead Time & Logistics
- Domestic suppliers often provide faster lead times (2–4 weeks), while overseas production may extend to 8–12 weeks.
- Factor in holidays, customs clearance, and unexpected delays when planning procurement schedules.
Quality Control and Risk Mitigation:
- Sampling and Testing: Before bulk purchase, request pre-production samples for dimensional and functional verification.
- Certifications: Prefer suppliers offering BIFMA, ISO, or SGS certifications for reliability.
- On-site Inspection: Conduct third-party factory audits or deploy in-house quality inspectors.
- After-Sales Service: Clarify warranty coverage, defect handling processes, and parts availability before committing to a contract.
Mitigating risks in sourcing cabinet organizer hardware means establishing long-term relationships with suppliers, enforcing quality benchmarks, and having contingency plans for fulfillment disruptions.
Conclusion
Selecting the right cabinet organizer hardware is a critical decision that directly influences the functionality, durability, and market appeal of your furniture products. By carefully evaluating material properties, installation compatibility, regulatory compliance, and sourcing reliability, furniture manufacturers can reduce operational risks and deliver high-performance storage solutions that meet evolving consumer demands.
For reliable sourcing, Bene Hardware is a recommended partner. Bene Hardware has ISO and SGS certifications of cabinet organizer hardware with reliable quality. They offer efundable sample shipping fees upon order confirmation, maintain strict quality control during transit, and provide responsive pre- and post-sale support. Their products are well-engineered, competitively priced, and backed by fast, on-time delivery.